Машины предназначены для высокоточного фигурного раскроя листового проката черных, цветных металлов и их сплавов методом плазменной или кислородной газопламенной резки. Толщина обрабатываемого проката от 1 до 300 мм, в зависимости от используемого технологического оборудования.
Предлагается ряд типовых портальных машин «Кристалл-1,5» «Кристалл-2,0» «Кристалл-2,5» «Кристалл-3,2» для раскроя листов шириной 1.5, 2.0, 2.5, 3.2 метра и длиной от 6 до 34 метра (определяется длиной рельсового пути).
В несущих конструкциях машины используются легкосплавные материалы, а также высокоточные направляющие, шариковинтовые пары, зубчатые рейки и колеса, которые поставляются ведущими зарубежными фирмами. Все это обеспечивает необходимую точность, легкость и жесткость конструкции рамы, а также стабильность работы на протяжении многих лет эксплуатации.
Высокомоментные вентильные двигатели немецкого производства и цифровой следящий привод, легкая и жесткая рама обеспечивает скорость перемещения портальной машины до 18 м//мин при высоких динамических характеристиках движения по контуру при обходе мелких деталей и острых углов.
В стойке управления используется промышленный компьютер класса Pentium III / Pentium IV, а также 15-ти дюймовый ЖК-монитор промышленного исполнения.
Новая конструкция и система управления обеспечивает установку до 5-и кареток (одна с плазменным резаком и до 4-х газовых с независимым управлением по высоте)., либо до 8-ми газовых кареток для раскроя листов на полосы.
Программные и аппаратные средства позволяют подключать портальную машину к локальной заводской сети. В этом случае осуществляется централизованная диагностика портальной машины, контроль работы оператора, загрузка управляющих программ, и т.д. с центрального компьютера (например компьютера технолога или начальника цеха).
Варианты технологического оборудования:
· «Плазма 400» – комплектация источником плазменной резки АПР-404 (ток резки – 200...400А), плазмотрон ПМР-74 (толщины от 4...40 мм) или ПМР-75 (толщины от 10...60 мм) с водяным охлаждением. Рабочий газ – воздух или кислород.
· «Плазма 400М» – отличается модифицированным источником АПР-404М с микропроцессорным управлением, расширенным диапазоном тока резки (80...400А) и плавным нарастанием тока при поджиге, что позволяет повысить ресурс работы расходных деталей плазмотронов и расширить диапазон разрезаемых толщины от 4 до 60 мм.
· " Kiellberg" - комплектация источником плазменной резки Kiellberg Fine Focus 800 (ток резки - 50...300А) c комплектным плазмотроном (толщины от 4...40 мм) с водяным охлаждением. Рабочий газ - воздух или кислород азот.
· «Плазма 150К» - источник плазменной резки АПР-150К (ток резки - 25...150А) может комплектоваться следующим плазмотронами:
· Cebora CP-160 (толщины 2...30мм);
· Hypertherm MAX-40 (толщины 1...5мм);
· Источник АПР-150К имеет плавную регулировку тока резки во всем диапазоне (25...150А), плавное нарастание тока при поджиге и высокую стабильность тока резки, благодаря высокочастотным ШИМ - преобразователям, используемым в схеме источника. Это позволяет получить отличное качество реза, устойчивый поджиг и горение плазменной дуги и большой диапазон толщины для резки, а также повысить ресурс работы расходных деталей плазмотронов.
· «Газ» - комплектация оборудованием для осуществления кислородной газопламенной резки с использованием в качестве режущего газа пропана, природного газа или ацетилена. Толщины от 2 до 300 мм. На каретке установлен резак для кислородной резки металла. Для управления технологией резки на машину устанавливается блок газовой резки БГР-047К. Блок осуществляет полный цикл управления газопламенной резкой, включая автоматический поджиг пламени, полное электронное управления расходом газов (автоматическая газовая консоль) и стабилизацию зазора между резаком и листом металла. Уникальность блока состоит в том, что имеется возможность задать параметры расходов газов отдельно для разных этапов резки (поджиг, подогрев, пробивка, резка). Тем самым повышается производительность резки, повторяемость технологического процесса, увеличивается стойкость расходных материалов.
Наиболее часто используемые резаки - Harris-198-2TAF, Harris-98-4F, Донмет РМ345, Эффект-М. Осуществляется резка металла в диапазоне толщин 3...200 мм (до 300 мм по спец. заказу).
· «Газ-2» На каретке устанавливается два резака. Один из резаков устанавливается вертикально. Специальная система крепления позволяет изменять угол наклона второго из резаков. В результате имеется возможность осуществлять как фигурную резку одним из резаков, так и прямолинейную резку с одновременным снятием фаски двумя резаками. В качестве резаков используется Harris-98-4F.
· «Газ-3» На каретке устанавливается трехрезаковый поворотный блок для кислородной резки. Система предназначена для осуществления фигурной резки по программе с одновременным снятием лицевой и/или тыловой фаски.Толщина металла при резке со снятием фасок- до 100 мм. Диапазон регулировки фасонных углов - 20...45 градусов.
Вращающаяся часть поворотного блока имеет бесконечный угол поворота.На каретке установлены система начального позиционирования резаков над листом и система стабилизации зазора между резаками и листом металла.
Качественная резка со снятием фасок может осуществляться только при правильно подобранном режиме резки. Режимы резки у центрального и боковых резаков сильно отличатся, так как различны как «эффективная толщина» металла, так и условия резки (например, степень подогрева металла). Уникальная электронная система управления трехрезаковым блоком позволяет управлять расходом режущих газов не только каждого резака в отдельности, но и отдельно для разных этапов процесса резки (поджиг, подогрев, пробивка, резка, факел). В качестве резаков используется Harris-98-4F.
Варианты комплектации портальных машин:
Машины могут быть укомплектованы различным технологическим оборудованием для обеспечения качественной термической резки различных металлов в широком диапазоне толщины.
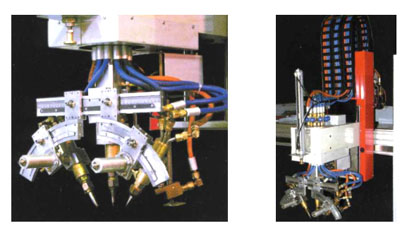
· "Одна каретка" - на портальной машине установлена одна каретка. На каретке расположен один держатель, в который может быть установлен один резак для плазменной или газовой резки. На фотографии портальная машина с одной кареткой и плазмотроном Kiellberg Fine Focus 800;
· "Одна каретка c двумя резаками" - на портальной машине установлена одна каретка. На каретке расположены два держателя резака. Один держатель для "рабочего положения" и один держатель для "транспортного положения". Резка производится одним резаком. Второй резак находится в транспортном положении. Переключение технологии резки осуществляется из диалогового меню системы управления портальной машиной. При смене технологии резки резаки меняются местами;
· "Две каретки с разным технологическим оборудованием" - наиболее распространенное исполнение - на портальной машине установлены две каретки. На одной каретке установлен плазменный резак, на второй каретке установлен газовый резак. На портальной машине установлены два комплекта технологического оборудования для осуществления газовой и плазменной резки. Переключение технологии резки осуществляется из диалогового меню системы управления портальной машиной. Резка осуществляется одним резаком. Неиспользуемая каретка выводится из зацепления и отводится в нерабочую зону. "рабочего положения" и один держатель для "транспортного положения". На фотографии изображена портальная машина с друмя каретками и оборудованием для плазменной (АПР-150К + плазмотрон Cebora CP-160) и газовой резки;
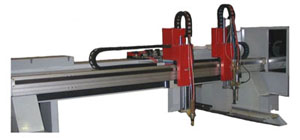
· "Многокареточное исполнение" - на портальной машине установлена одна каретка для плазменной резки и до 4-х кареток с газовыми резаками. Плазменная резка осуществляется одним резаком. Остальные резаки выводятся из зацепления и отводятся в "парковочную зону". Газовая резка может осуществляться несколькими резаками синхронно. При этом увеличивается производительность работы портальной машины. Оборудование, установленное на машине позволяет управлять технологическим процессом резки одновременно на нескольких резаках. На фотографии изображена портальная машина с четырьмя каретками. На всех каретках установлены газовые резаки. На одной из кареток также установлен плазменный резак ПМР-74 (в транспортном положении);
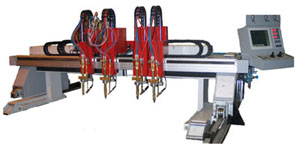
Система управления портальной машиной «Кристалл»:
Система управления портальной машиной "Кристалл" нового поколения обладает рядом новых технических, технологических и эргономических решений, некоторые из которых не имеют аналогов не только в России, но и в мире.
· Система экранного меню и диалоговых окон полностью русифицированы, что позволяет освоить управление портальной машиной людям без компьютерного образования;
· На пульте оператора установлена специализированная русифицированная пленочная клавиатура пыле-влаго-масло стойкого исполнения;
· Ручное управление перемещением машины и высотой резака осуществляется с помощью бесконтактных аналоговых джойстиков, что позволяет плавно менять скорость перемещения машины в ручном режиме и с легкостью позиционировать резак в любую точку разделочного стола;
· Управляющий компьютер портальной машины связан с микроконтроллерами электроавтоматики с помощью оптического волокна, что позволило: достичь беспрецедентной надежности и устойчивости системы в условиях высокого уровня электромагнитных помех создаваемых в плазменной дугой, при необходимости комплектовать портальную машину выносной стойкой управления и устанавливать ее на расстоянии до 50 метров от портальной машины;
· Модульное устройство блоков и узлов системы управления позволяет наращивать количество технологического оборудования и иметь: до 24-х осей управления движением портальной машины, до 8-и блоков управления газовой резкой, при установке выносной стойки управления иметь до 4-х пультов управления портальной машиной;
· Дискрета управления перемещением портальной машиной уменьшена до 4,9 микрона, что позволяет использовать данную систему в комплексах, требующих значительно более высокие точностные и динамические показатели, чем машины плазменной и газовой резки;
· Скорость перемещения портальной машины увеличена до 14м/мин (при необходимости достигается скорость до 20 м/мин);
· Система управления портальной машиной имеет встроенную поддержку локальных вычислительных сетей по протоколу TCP-IP, что позволяет: осуществлять диагностику всех узлов и блоков портальной машины через локальную или глобальную вычислительную сеть (в том числе через Internet), копировать и считывать управляющие программы с управляющего компьютера портальной машины через компьютер, подключенный к сети, получать полный отчет о работе портальной машины и действиях оператора с любого компьютера, который подключен к сети и имеет соответствующие коды доступа (например с компьютера технолога, мастера, начальника цеха и т.п.);
· Имеется дополнительное программное обеспечение, позволяющее иметь доступ, управление, диагностику, копирование управляющих программ через беспроводные сети (WiFi) с наладонного компьютера (Pocket PC);
· Новые возможности блока газовой резки позволяют достичь оптимального управления технологическим процессом газовой резки, снизить расход газов и повысить качество реза и производительность резки;
· Имеется автоматическое управление высотой резака в процессе поджига и пробивки (опускание резака, поджиг дуги (газового пламени) автоматическая пробивка металла, выход на заданную высоту и осуществление резки со стабилизацией зазора между резаком и листом металла);
· Управление портальной машиной согласно управляющей программе;
· Полное программное управление технологическим процессом термической резки для плазменной и газовой резки металлов (включая управление и стабилизация расхода режущих газов в зависимости от технологического режима);
· Формат управляющих программ (УП): ISO ESSI, G-функции;
· Загрузка УП может производиться: с внутренней флэш-памяти портальной машины (Объем флэш-памяти позволяет хранить в памяти до нескольких десятков тысяч УП карт раскроя), с USB-флэш диска, с локальной или глобальной вычислительной сети, с дискеты 3,5 дюйма, с пульта оператора, клавиатуры пульта инженера;
· При загрузке в диалоговом окне отображается список УП, находящихся на диске, размер файла УП, графическое отображение карты раскроя текущей УП.
· Встроенная в систему сетевая поддержка позволяет производить контроль действий оператора, диагностику узлов и блоков портальной машины, загрузку и выгрузку управляющих программ, а также управление портальной машиной через компьютерную сеть (локальную или глобальную - Internet).
Режимы выполнения управляющей программы.
Выполнение управляющей программы возможно в следующих режимах:
· резка;
· черчение;
· вся программа или пошаговое выполнение;
· движение «вперед» или «назад» по программе.
Возврат на программный контур:
В любой момент оператор имеет возможность остановить выполнение программы, нажав клавишу «СТОП», отвести в ручном режиме резак с контура управляющей программы (например, для осмотра резака, его переборки, замены электрода или т.п.). При необходимости можно отключить питание портальной машины (например, в случае окончания рабочей смены), затем включить его снова. После завершения работ с резаком оператор нажимает кнопку «ВОЗВРАТ» на пульте оператора, при этом система автоматически возвращает резак в исходное положение на контур управляющей программы. После нажатия кнопки «СТАРТ» продолжится выполнение программы с точки остановки.
Коррекция неточной укладки листа:
Лист металла был уложен на разделочный стол с перекосом и карта раскроя не вписывается в лист; кран занят; оператор вынужден с помощью подручных средств выравнивать положение листа на разделочном столе - достаточно типичная ситуация на предприятиях. Для такой ситуации разработан режим коррекции неточной укладки листа.
В этом режиме оператор с помощью ручных перемещений резака указывает две точки на краю листа. Программа по координатам этих точек определяет угол поворота листа и поворачивает карту раскроя управляющей программы на такой же угол.
Система управления портальной машиной (СУПМ) имеет развитую систему защиты от ошибочных действий оператора:
· Блокировка перемещения портальной машины при наезде на концевые выключатели;
· Блокировка запуска выполнения УП при несоблюдении необходимых условий (отсутствие прохождения контрольных сигналов от технологического оборудования, датчики расхода охлаждающей жидкости, датчики давления воздуха, режущих и подогревающих газов, концевые выключатели, датчики положения ротора двигателя перемещения портальной машиной по координатам X1,X2,Y);
· Блокировка при ошибке расположения программы раскроя на разделочном столе;
· Блокировка при ошибках в исходной УП.
Система подготовки управляющих программ «Техтран»
Программа предназначена для комплексного решения задачи раскроя листового материала. Она сочетает возможности системы подготовки управляющих программ с функциями организации производственного процесса.
Использование базы данных:
Программа объединяет традиционные средства программирования обработки «Техтрана» с базой данных. На базу данных возлагается не только задача управления различными данными, но и управление работой системы в целом. В базу данных заносятся детали, которые могут быть построены средствами «Техтрана» или импортированы из другой системы.
Задание на раскрой
Из деталей, которые необходимо изготовить, формируется задание на раскрой. Затем в задание на раскрой включаются листы для изготовления деталей. Программа обеспечивает возможность автоматического и ручного размещения деталей задания на раскрой на листах. При этом программа отслеживает количество неразмещенных деталей и возможность изготовления детали из выбранного листа.
· Автоматическое размещение деталей на листе. В режиме автоматического размещения программа укладывает детали задания на листы оптимальным образом, выдерживая заданные расстояния до края листа и между деталями.
· Ручное размещение деталей на листе. В этом режиме деталь выбирается из списка неразмещенных деталей задания на раскрой и укладывается на лист, а затем перемещается на свободное место средствами графического редактора. Сочетание автоматического и ручного размещения деталей дает возможность выгодно использовать преимущества каждого режима для наиболее эффективной работы.
· Контроль перемещения деталей. В режиме ручного размещения программа контролирует соблюдение требуемых расстояний между деталями и от деталей до края листа. Имеется возможность располагать детали вплотную друг к другу. Имеются режимы контроля перемещения деталей:
· Строгий контроль перемещения деталей. Включение этой функции позволяет перемещать детали по листу на экране монитора, как реальные предметы, для которых другие детали и край листа являются непреодолимым препятствием;
· Предупреждающий контроль перемещения деталей. При предупреждающем контроле перемещение деталей не ограничивается свободной областью листа. Однако при попадании в зону перекрытия с другими объектами происходит диагностирование недопустимого расположения путем изменения цвета перемещаемой детали;
· Перемещение деталей до упора. Эта функция дает возможность прижать деталь вплотную к самому краю свободной области листа. Иными словами, при данной операции происходит перемещение детали в некотором направлении до тех пор, пока она не упрется в деталь или край листа;
· Копирование деталей вплотную друг к другу. При копировании деталей в этом режиме автоматически определяется расстояние, на которое может быть перемещена деталь в заданном направлении, чтобы детали располагались вплотную друг к другу;
· Выравнивание деталей по прямой. Такая возможность полезна при расположении деталей под обработку сквозным резом.
Программирование обработки
После того как детали размещены на листе, программируется обработка. В простейшем случае достаточно последовательно указать обрабатываемые контуры деталей. Программа строит траекторию движения инструмента с учетом необходимых поправок, формирует подходы, отходы и вспомогательные перемещения инструмента, команды включения и выключения резака, подачи, коррекции и т.д.
· Подход и отход. Предусмотрена возможность разнообразной настройки способов подхода к обрабатываемому контуру (по прямой, по дуге, по нормали, по касательной и т.п.), выбора точки подхода (автоматически или явно) и режимов работы резака на различных стадиях обработки;
· Перемычки. На контуре детали могут быть выделены непрорезаемые участки - перемычки. При построении траектории программа автоматически формирует в таких местах команды включения и выключения резака и встраивает участки подхода и отхода;
· Мостики. Мостики между деталями позволяют обрабатывать несколько деталей без выключения резака. Задание точек перехода траектории от одной детали к другой производится после размещения деталей и учитывается при построении окончательной траектории резака;
· Автоматическая обработка. Режим автоматической обработки дает возможность максимально упростить программирование обработки большого числа деталей. Программа сама назначает последовательность обхода деталей на листе и выполняет обработку. Различные стратегии обхода деталей обеспечивают соблюдение необходимых условий обработки.
Разделка кромок под сварку
Разделка кромок под сварку может производиться на машинах термической резки, оснащенных трехрезаковыми блоками. В программе предусмотрена возможность обработки деталей как с постоянными, так и с переменными фасками. Постоянная фаска характеризуется постоянством лицевых и тыловых углов и высот по всей длине. Переменная фаска характеризуется равномерным изменением угла и высоты по длине.
Программа автоматически встраивает в траекторию движения резака специальные участки - окна вреза в местах включения боковых резаков и петли разворота резаков, которые обеспечивают правильную ориентацию боковых резаков и соблюдение необходимых условий обработки. Положение окон вреза может быть изменено с помощью графического редактора.
Разделочный стол и система вытяжной вентиляции
Разделочный стол по размеру должен соответствовать максимальному размеру обрабатываемого листа металла. В настоящее время поддерживаются две модели столов - с горизонтальной и вертикальной вытяжкой задымленного воздуха.
Стол с горизонтальной вытяжкой
Cтол представляет собой единый сварной короб и из-за своих габаритов может быть изготовлен только на месте эксплуатации по чертежам, предоставляемым нашим предприятием. Стол устанавливается на ровный бетонный пол и фиксируется анкерами для предотвращения смещений при случайных ударах при погрузке разрезаемых листов. Для облегчения периодической чистки стола от шлама в короб вставляются съемные секции со сменными ребрами, на которые при резке укладывается раскраиваемый лист металла. Сменные ребра прямоугольной формы изготавливаются из листового металла и являются расходным материалом, нуждающимся в замене по мере износа. Средний срок службы от - 3 до 6 месяцев, в зависимости от загрузки машины. Толщина ребер составляет от 2 до 12 мм в зависимости от толщины разрезаемого металла.
Стол с горизонтальной вытяжкой может быть изготовлен как в «сухом» исполнении, так и с заполнением водой для плазменной резки. Вода под разрезаемым листом позволяет собрать до 90% выделяющегося дыма. Вода постепенно накапливает кислотность из-за растворения окислов азота, образующихся в плазме, и нуждается в периодической нейтрализации и замене. Даже при использовании водяного стола использование вытяжной вентиляционной системы обязательно. Вентиляционная система изготавливается на нашем предприятии и поставляется отдельно. Забор задымленного воздуха осуществляется непосредственно из зоны резки из-под разрезаемого листа и над листом. Движение воздухозаборников вместе с машиной осуществляется с помощью специальных желобов, закрытых с одной стороны транспортерной лентой. Лента поднимается в зоне резки специальными механизмами, установленными непосредственно на подвижной части машины. В зависимости от размеров разделочного стола в комплект поставки включаются 2 или 4 вытяжных вентилятора среднего давления, гибкие воздуховоды для быстрого монтажа, хомуты и крепеж.
Стол с вертикальной вытяжкой
Этот тип столов отличается лучшим удалением задымленного воздуха и имеет встроенную в стол вытяжную вентиляцию. Стол состоит из отдельных 2-метровых секций, целиком изготавливается на нашем предприятии и поставляется отдельными секциями. Каждая секция имеет массу около 2,5 т и устанавливается на ровный бетонный пол на регулируемые по высоте опоры, с последующей фиксацией к полу анкерными болтами. Стол также оснащен съемными секциями с аналогичными ребрами. Забор воздуха осуществляется только в зоне резки. Переключение зон осуществляется системой заслонок с пневмоцилиндрами, что позволяет снизить нагрузки на подвижную часть портальной машины и улучшить ее динамические характеристики. В комплект поставки стола также входят вентиляторы, воздуховоды, крепеж и цанговые анкера.
Технические характеристики
Наименование параметра
|
Значение
|
Напряжение питания, В
|
3х380 (50 Гц)
|
Скорость перемещения м/мм
|
0-18
|
Регулировка скорости движения
|
плавная
|
Кол-во плазменных или кислородных резаков
|
|
Стандартное исполнение
|
до 4
|
по заказу
|
до 8
|
Вертикальный ход резака, мм
|
300
|
Геометрическая точность при прочерчивании по ГОСТ 5614-74
|
Выше 1 класса точности
|
Внутренняя дискрета управления, мкм
|
<10
|
Скорость позиционирования, м/мин
|
до 24
|
Скорость резки, м/мин
|
0,02...6
|
Точность позиционирования, мм
|
± 0,15
|
Точность обхода острых углов, мм
|
± 0,2
|
Величина вертикального хода (Электропривод), мм
|
300
|
Формат управляющей программы
|
Код ISO, формат кадра ESSI
|
Геометрическая точность при прочерчивании
|
Согласно ГОСТ 5614-74
|
Комплект поставки
Портальная машина включает в себя рабочее место оператора, управляющий компьютер (с дисководом 3,5 дюйма, портами USB и необходимыми сетевыми интерфейсами для загрузки управляющих программ), 15-дюймовый ЖК монитор, все необходимые блоки, узлы и технологическое оборудование для обеспечения качественной термической резки металла, в том числе систему слежения за высотой резака, датчики контроля состояния машины.
В перечень поставки может быть включен комплект ЗИП для ремонта портальной машины методом замены блоков силами обслуживающего персонала, дополнительный персональный компьютер с установленным программным обеспечением для подготовки управляющих программ с оптимизацией раскроя и ведением базы учета листов, деталей, деловых отходов. Комплект поставки, исполнение машины, ЗИП, количество расходных материалов согласовывается с потребителем в соответствии с условиями работы и загрузки машины.